https://bker001.tistory.com/458
[직무분석] 기계설계란 + 기계설계를 비추하는 이유
https://bker001.tistory.com/447 [직무 분석] 기계공학전공의 생산관리 이번에 생산관리 부문으로 IPP에 신청해서 면접준비를 하게 되었었는데, 아무래도 생산관리는 산업공학전공인 분들이 많이 지원하
bker001.tistory.com
기계설계에 이은 생산기술입니다.
생산기술은 지식적으로 생산관리와 비슷할 정도로 알아야 할 정보가 많은 것 같습니다.
그래서 이번에는 퀄리티 있는 영상을 보면서 영상에 나온 것들을 정리하면서 생산기술이 뭔지 알아보겠습니다.
생산기술이란 생산라인의 트러블슈팅 및 생산CAPA를 증대시키기 위한 업무를 수행하는 직무입니다.
풀어서 이야기하면,
생산라인의 시스템에서 발생하는 복잡한 문제들을
종합적으로 진단 및 관리하고, 생산능력을 증대시키기 위한 업무를 수행하는 직무
입니다.
생산라인을 관리하기 때문에, 개조시에 현재 방식 대비 어떻게 바꿔야 작업자가 편하고,
Cycle time을 단축시킬 수 있는지 생각하여 산성 증대를 위한 직무입니다.
생산기술에서는 생산성 향상 + QCD의 최적화가 중요합니다.
1. 트러블 슈팅 troubleshooting : 시스템에서 발생하는 복잡한 문제들을 종합적으로 진단 및 처리함. 즉 불량처리
2. Capa, Capacity : 생산능력
3. QCD란, Quality / Cost / Delivery, 품질/원가/납기.
① 꼭 알아두어야 하는 용어 - 택트타임, 싸이클타임, 리드타임
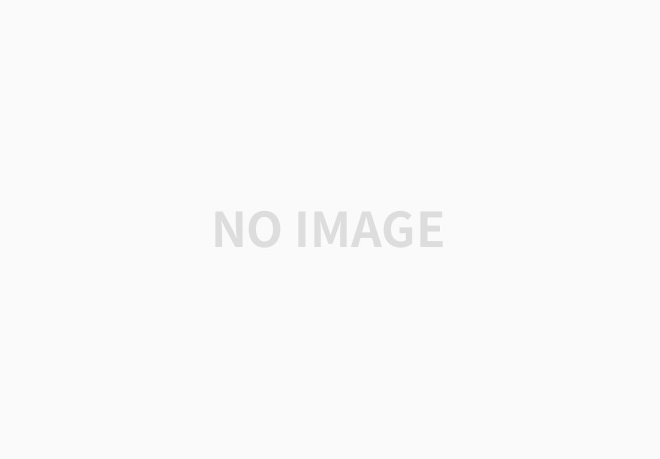
Takt Time(택트타임) : 제품 한 개를 생산하는데 필요한 시간
Takt Time = 작업 가능한 생산 시간 / 필요 생산 수량
Eg, 하루 100시간 동안 100개의 제품 생산을 요구할 시 = 100시간 / 100개 = 1시간
Cycle Time(사이클타임) : 단위공정 한 단위를 완성하는데 걸리는 시간, 원자재의 투입부터 완성까지의 시간
Cycle Time = 순 생산 시간 / 순 생산 시간 동안 생산된 수량
Eg, 100시간을 들여 100개 생산 = 100시간 / 100개 = 1시간
Lead Time(리드타임) : 주문이 접수된 후 고객에게 배송될 때까지의 시간
Lead Time = 주문 납품 시간 - 주문 접수 시간
Eg, 2021년 1월 4일 주문 접수 후 2021년 1월 7일 납품 완료 = 2021/1/7 - 2021/1/4 = 3일
② 생산기술의 3가지 확보
1) 품질의 확보
3정 5S를 통한 깨끗한 현장 - 눈에 보이는 관리가 중요합니다.
평균화 및 평준화 생산으로 표준화 및 유지관리를 진행합니다.
2) 원가 확보
평선효율 향상
3불(불합리, 불균일, 불필요) 제거!
자재재고와 부자재비의 감소
3) 납기의 확보
평균화 및 평준화 생산
JIT에 의한 재고관리
공정 단축 (모듈화 및 레이아웃 개선)
공정에서 발생하는 문제점 개선
3정 5S
3정 : 정품, 정량, 정위치로 필요한 물건을 찾기 쉽게, 사용하기 쉬운 상태로 해두는 정돈의 기본.
5S : ① 정리 : 필요한 것과 필요 없는 것을 구분하여 필요한 것 이외 두지 않는다
② 정돈 : 필요한 것은 누구나 바로 꺼내서 쓸 수 있는 상태로 하는 것 - 찾는 시간 과다소모, 재고파악 문제
③ 청소 : 직장을 쓰레기가 없고, 더럽혀짐 없이 함. - 불량 발생의 원인, 설비고장율 증대
④ 청결 : 정리, 정돈, 청소 철저히 - 불합리 개선시 시간 소요
⑤ 습관화 : 정해진 것을 정해진 대로 올바르게 실행 할 수 있도록 습관하는 것
= 결국 이 모든 것을 내 몸에 채득하여 습관처럼 하겠다.
평균화 생산 / 평준화 생산
평균화 생산 : 매일매일의 생산량을 균일화시켜서 거의 동일한 수량의 생산이 되도록 하는 것.
평준화 생산 : 모든 작업장에 균일한 부하를 부과하고자 하는 것으로 생산하고자 하는 제품을 적절히 혼합하고, 조절하여 생산하는 수량과 종류의 평균화
= 생산 부하를 평준화시킴.
③ 공정 개선을 위한 노력점
문제가 보일 때 까지 4M1I를 관찰하여 관리합니다.
이러한 공정개선을 위해서는 낭비가 없어야합니다.
3불(불필요 , 불균일, 불합리)를 제거하여 개선하고, 7대 낭비 개선방안을 통해 노력점을 확인합니다.
4M1I
Man 작업자
Machine 설비
Method 공정
Material 재질변경 및 설계변경 등.
Information 기본 정보
- 과잉생산 : 평균화, 평준화 생산 / 준비 교체시간 단축
- 재고관리
- 운반 : 레이아웃 (제조공정의 흐름 및 생산량, 작업성, 물류, 인원등을 고려하여 설비 배치하는 것) 개선, 흐흠 생산등
- 불량제조 : 풀프루프 (무의식 중 일으키는 실수 방지 및 즉시 알게하여 조치토록 함, 불량을 미연에 방지하는 것)
개선, 이는 인명 피해 뿐 아니라 생산성에도 문제를 일으키기 때문에 사고를 미연에 방지하는 것이 중요.
- 가공자체 : 공정설계의 적정화 및 자동화
- 대기 : 준비 교체시간을 단축
- 부가가치를 창조하지 않는 동작 : U자형 설비 배치등
자동차 쪽 생산기술
가공과 조립으로 크게 나뉜다. 가공라인은 6축로봇,
MCT(머시닝센터)등의 공작기계로 가공을 한다.
칩이 제거 되지 않은 상태로 조립이 되면 유압을 형상할 수 있는
고무류에 데미지가 발생한다. 그래서 칩제거가 중요합니다.
조립 (가공 후 조립)은 보통로딩, 언로딩 부분만 작업자가 하고
나머지는 6축 로봇, 컨베이어 벨트, 로터리 인덱스, 유공압 실린더,
각종 테스터기(진공리크, 에어리크)등을 활용합니다.
*PLC 개념이 중요하기에 PLC에 대해 공부하는 것을 추천합니다.
https://e-koreatech.step.or.kr/
STEP
e-koreatech.step.or.kr
*생산기술 실제 자동차 회사 업무체계
1. 디자인 리뷰 - 신차 개발 단계에서 도면 검토, 설계팀에 도면 수정 검토 요청, 양산 차종 도면 검토등
2. 4M 개발(신차) - PILOT(양산 전 시험차) 샘플 제작, 감사 준비 및 대응, Error Proof : 불량을 검출해서 라인에서 배출 시킴으로 불량이 유출되지 않도록 자동검증하는 장치들, 이런 Error proof 유효성을 검토
3. 4M 관리 - 공정개선, 기구 개선 및 제작, 실적 정리, 작업 loss 원인 조사
4. 각종 감사대응 및 실시
5. 벤치 마킹 - 타사 제품 벤치마킹
6. 고객 불량 대응
생산기술+
1. 시작기술(선행생산기술)
신모델 개발 양산 전에 St 분석 / Lob(Line of balance,
반복적인 작업의 흐름을 시간에 따른 진행상황의 함수로 직선으로 나타내는 기법) 점검
양산 확정 전 예상되는 문제를 선행적으로 검토, 시험하여 발생되는 손실을 최소화하는 것.
개발단계 샘플 제작 및 관리 시작함.
2. 장비기술(양산생산기술)
생산성 향상 및 설비개선 - 양산을 더 효율적으로 하기위해 개선
- 최적의 투자효율을 확보, 신규 공장 설비 / Layout 제안
- 공장 증설시 증설 효율을 극대화 하는 역할.
- 최적의 투자 확보, 신규 공장에 대한 설비 및 공간 활용을 극대화하기 위해 레이아웃 제안.
- 설비 트러블 발생 시 조기 대응으로 양산이 안정적으로 진행되게 한다.
으어 엄청 깁니다만 거의 정리했습니다.
마지막으로 정리를 다시 해보면,
목표 : 개발된 제품을 안정적으로 싸게, 빠르게 생산될 수 있도록 하는 것.
효율적으로 생산할 수 있는 인프라를 설계하는 것.
라인을 최적화하여 효율적 양산, 시간과 비용 적게하여
회사의 이익을 위해 원가절감을 추구하는 것
이 되겠습니다. 생각보다 공부할게 많지만서도 PLC 공부라는 가이드가 있으니
해볼만 하다는 생각도 듭니다.
노력해봐야겠습니다.
참고 사진 및 영상 링크
출처: https://ngroovy.tistory.com/5122 [싸굴다방 DJ:티스토리]
https://www.youtube.com/watch?v=f7Bk-50LI5E&t=524s
'취업 관련 준비 > 직무분석' 카테고리의 다른 글
[직무분석] 기계설계란 + 기계설계를 비추하는 이유 (0) | 2024.02.18 |
---|---|
[직무 분석] 기계공학전공의 생산관리 (1) | 2024.02.14 |